Leonardo a Nerviano, da qui parte la fabbrica del futuro
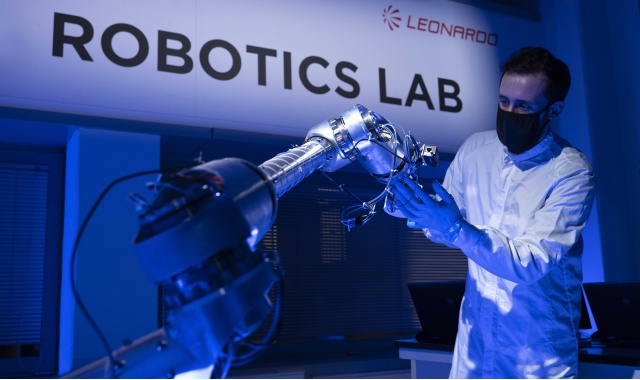
Charlie Chaplin in Tempi Moderni mostrava gli operai come vittime dell’avanzamento tecnologico. E invece gli stabilimenti produttivi del futuro assumono la forma di un’organizzazione altamente automatizzata dove le risorse utilizzate nei processi operativi sono strettamente interconnesse e dove, grazie alle tecnologie digitali, le imprese manifatturiere sono in grado di produrre con maggiore efficienza, secondo standard qualitativi sempre più elevati e nel rispetto delle persone e dell’ambiente.
In Leonardo – in modo particolare negli stabilimenti di Nerviano (Milano) e di Cisterna di Latina (Roma) – questa rivoluzione ha subito un’accelerazione grazie a soluzioni digitali sempre più avanzate. Questo nell’ambito di “Factory of the future”, iniziativa avviata nel marzo 2021 dalla divisione Elettronica di Leonardo con il supporto del Politecnico di Milano, che ha definito un nuovo approccio industriale integrato, costituito da un insieme eterogeneo di tecnologie digitali innovative distribuite lungo la catena del valore e l’intero ciclo di vita del prodotto, per adempiere ai requisiti di trasformazione digitale richiesti dai nuovi programmi internazionali strategici. Primo fra tutti questi, il “Future Combat Air System”, un sistema di sistemi imperniato su tecnologie emergenti con al centro una piattaforma aerea di sesta generazione, che ridisegnerà le future capacità operative e industriali dell’intero settore aerospaziale.
Una serie di fattori esterni a livello mondiale ha poi contribuito a imprimere un’ulteriore forte spinta verso la digitalizzazione e verso la sostenibilità ambientale e d’impresa, dando luogo alla definizione del piano europeo “Next Generation EU”, declinato in Italia nel “Piano Nazionale per la Ripresa e Resilienza” e in Leonardo nel piano strategico “Be Tomorrow - Leonardo 2030”. Da qui prende anche le mosse il nuovo approccio industriale Factory of the Future, caratterizzato dall’utilizzo pervasivo di tecnologie digitali connesse e interoperabili, che si realizza nella completa integrazione di tutti i fattori che concorrono alla creazione del valore di una fabbrica.
Il framework del progetto si basa su 10 stream, o filoni, distinti ma tra loro interconnessi, come la tracciabilità logica e fisica delle tecnologie; lo scheduling per la razionalizzazione delle risorse e la simulazione di scenari produttivi; l’automazione dei processi; la logistica avanzata dei materiali, ad esempio mediante magazzini intelligenti; l’implementazione di tecnologie innovative quali quelle dell’additive manufacturing, non solo in campo meccanico, ma anche in campo elettronico. Non da ultimo, l’utilizzo di tecniche di realtà aumentata e virtuale a supporto dell’esecuzione di operazioni a elevata complessità.
A queste si aggiunge l’integrazione verticale e orizzontale digitale delle informazioni che vengono raccolte in tempo reale nellediverse fasi di lavorazione, aggregate e condivise nei diversi livelli gerarchici dell'azienda, tra le differenti funzioni e lungo tutta la supply chain. L’aggregazione e la corretta rappresentazione di questa mole eterogenea dei dati generati dalla fabbrica è possibile grazie alle tecniche di Big Data intelligence, elemento imprescindibile per estrarre valore aggiunto dai dati. Nella fase di design di un prodotto, infine, è fondamentale l’implementazione del digital twin, ovvero la creazione di un “gemello virtuale” equivalente a quello fisico, sul quale le simulazioni consentono l’analisi e la rimodulazione dei processi industriali.
In questo framework ben strutturato ci sono due direttrici fondamentali: la sostenibilità ambientale e l’apprendimentocontinuo delle persone che vi operano. La fabbrica del futuro è infatti inclusiva e si fonda sulla convivenza di più generazioni. Ed è proprio la formazione costante e i processi di upskilling e reskilling del personale che consentono di non lasciare indietro nessuno.
Lo stabilimento Leonardo di Nerviano ha definito una precisa roadmap di trasformazione digitale. La missione del sito lombardo è lo sviluppo e la produzione di sistemi radar e di computer avionici per velivoli ed elicotteri, per impieghi sia civili sia militari. A Nerviano vengono anche progettati e realizzati diversi equipaggiamenti per lo Spazio, tra cui orologi atomici, sistemi robotici e di trivellazione e unità di distribuzione della potenza, installati sui satelliti delle principali missioni dell’Agenzia Spaziale Europea (ESA) e della NASA. A Nerviano vengono prodotte, inoltre, schede elettroniche per applicazioni avioniche e spaziali e per la produzione delle PVA (PhotoVoltaic Assembly), i pannelli solari che forniscono ai satelliti in orbita l’energia elettrica di cui hanno bisogno nel corso della loro vita operativa.
Lo stabilimento ha fatto suo il framework di Factory of The Future declinandolo in progetti portati avanti da giovanissimi “digital team”, gruppi di lavoro con età media inferiore ai trent’anni, affiancati dall’expertise di colleghi con elevata seniority.
E alla base di tutto ciò vi è lo sviluppo della digital backbone, l’infrastruttura digitale che mette in comunicazione le diverse aree di processo e l’ecosistema di cui la fabbrica è parte fondamentale, al fine di valorizzare i dati prodotti e raccolti nelle attività svolte lungo la catena del valore.
Un esempio per rendere tangibile cosa è possibile fare grazie ai nuovi processi e alle tecnologie: se l’Agenzia Spaziale Europea è chiamata a effettuare un’ispezione al microscopio di schede elettroniche prodotte per applicazioni Spazio, nella fabbrica del futuro ciò sarà possibile mettendo la scheda nelle mani di un robot collaborativo integrato con un sistema di visione ad alta risoluzione e con un modulo di realtà aumentata controllato da remoto, ad esempio direttamente da una delle sedi dell’ESA, con vantaggi evidenti in termini di tempi e di costi ma con la stessa efficacia.
Altro passo verso il futuro è rappresentato dal progetto di manutenzione predittiva con l’installazione di una vasta gamma di sensoristica IoT (Internet of Things) per monitorare in tempo reale una serie di parametri che vanno dall’assorbimento di corrente al flusso di aria compressa o dal rumore ambientale all’illuminazione, con lo scopo di predire potenziali malfunzionamenti o guasti ai macchinari ben prima che questi si verifichino.
Ultimo, ma non per importanza, progetto avviato a Nerviano è la “Manufacturing Academy”, uno spazio di lavoro flessibile e riconfigurabile dove svolgere formazione teorica e pratica sulla base di un ampio catalogo di corsi, effettuare brainstorming, sviluppare soluzioni innovative, avviare sperimentazioni tecnologiche.
© Riproduzione Riservata